Polestar et Bcomp : la fabrication de notre tissu intérieur emblématique
L’industrie automobile est soumise à des bouleversements sismiques. Les groupes motopropulseurs, la conduite autonome et les systèmes d’infodivertissements sont en train de transformer notre vision de la mobilité. Pour ne pas être laissés derrière, les designers intérieurs et les usines de textile proposent leurs propres innovations et s’empressent de mettre au point de nouvelles matières durables, mais luxueuses. Et c’est au milieu des Alpes suisses que nous pensons avoir trouvé cela.
Au cœur de Fribourg en Suisse, une révolution tranquille était en cours. Bcomp, une entreprise fondée en 2011, développait des fibres de lin comme tissus de renforcement qui semblaient prêts à redéfinir le luxe et le design durable. Faisant d’abord des vagues dans le monde du ski, où leurs tissus en lin amélioraient les performances, tout en offrant une meilleure réduction des vibrations, le parcours de Bcomp a pris une direction inattendue lorsque Polestar a sollicité un partenariat avec elle.
La magie réside dans les matières de Bcomp : ampliTex™ et powerRibs™. La première est faite de fibres de lin tissées qui réduit non seulement les vibrations et le poids total, mais ajoute également une couche visuelle attrayante. L’autre s’inspire de la structure veineuse des feuilles et forme une structure en 3D sur les panneaux, augmentant drastiquement la solidité et la rigidité, tout en réduisant le poids.
« Lorsque nous avons vu le matériau pour la première fois, nous avons tout de suite su que cette technologie s’alignerait parfaitement avec les objectifs de Polestar », se rappelle Ross Kelk, directeur de la recherche et du développement des revêtements intérieurs et chef de programme industriel de l’équipe anglaise de développement de Polestar. « Depuis le début, nos compagnies partagent les mêmes buts et valeurs, et le même état d’esprit. »
Cependant, au début, nous étions incertains de la façon dont le matériau serait employé et de l’endroit où il apparaîtrait. De plus, l’apparence de la matière ne s’accordait pas avec notre idée de performance luxueuse que nous voulions présenter dans nos voitures Polestar. « Avec l’équipe de conception, nous avons expérimenté, joué et essayé différentes choses », explique Ross. Cette approche expérimentale a été appliquée aux matières, ainsi qu’à notre perception globale du luxe. « Habituellement, les fabricants associent le luxe à l’exclusivité des matériaux, comme le cuir et le bois plaqué, et beaucoup de décorations. Toutefois, nous voulions mettre la matière de l’avant et la présenter ouvertement, et faire de la durabilité une expérience tangible et exclusive. »
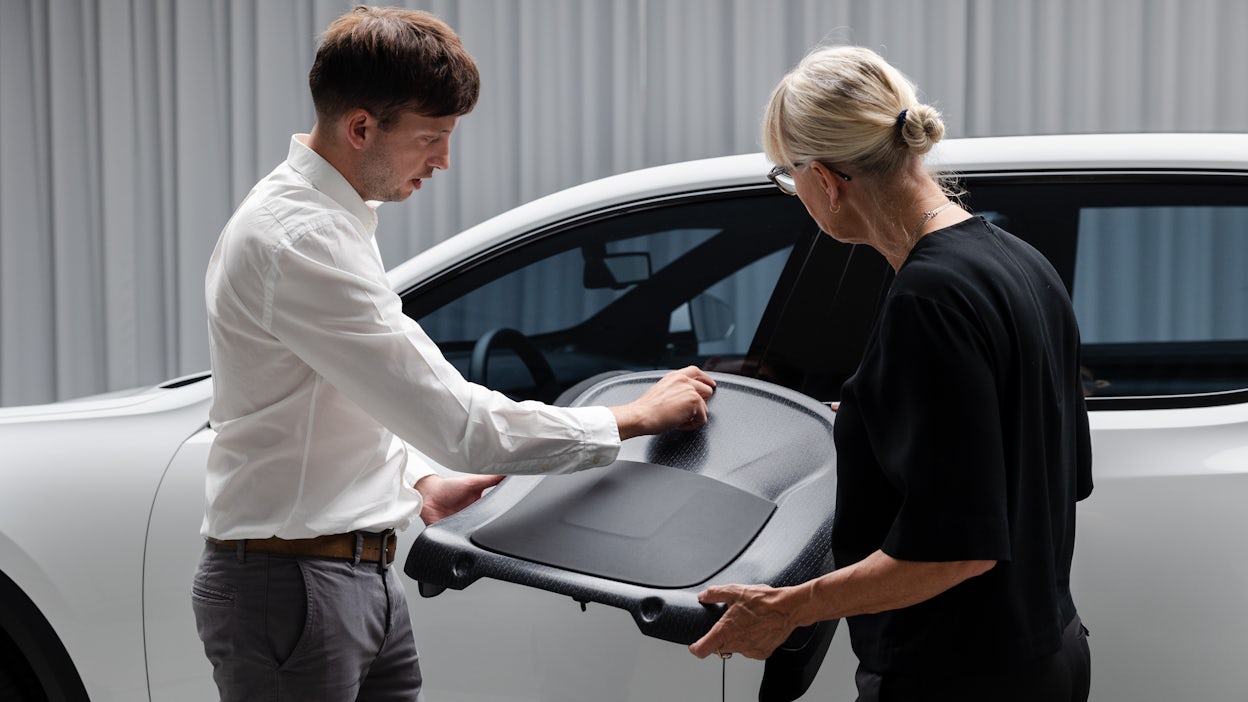
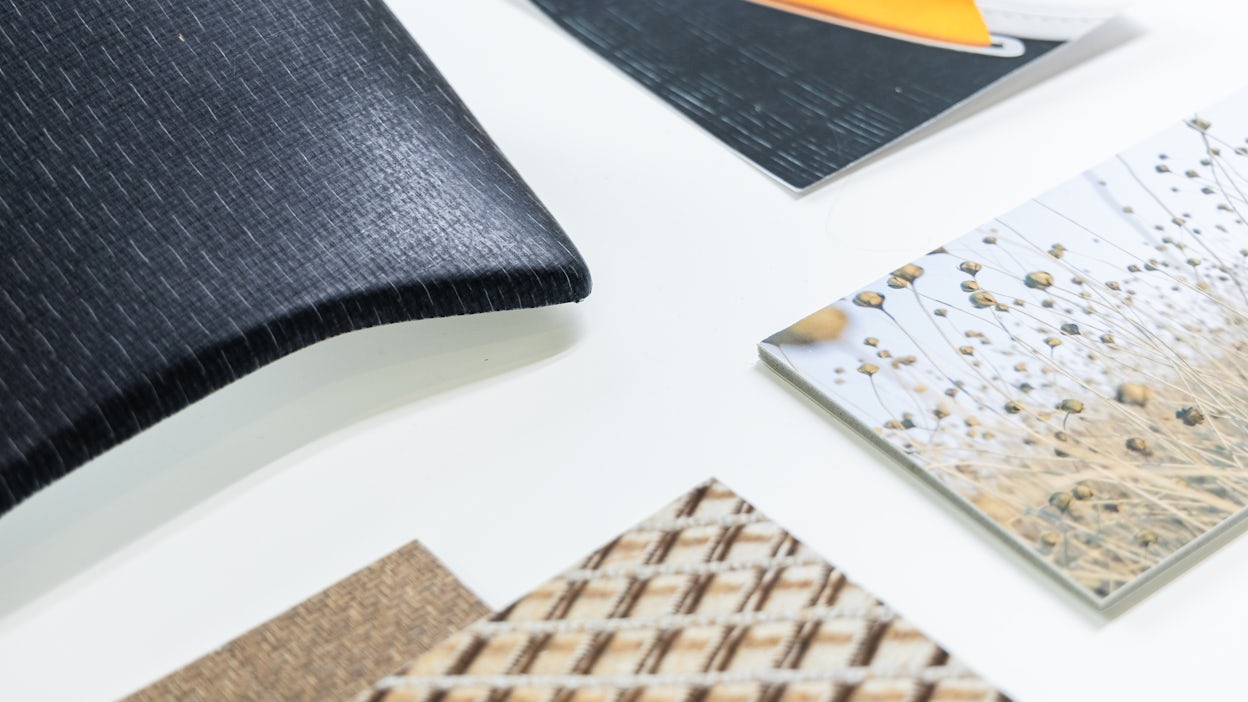
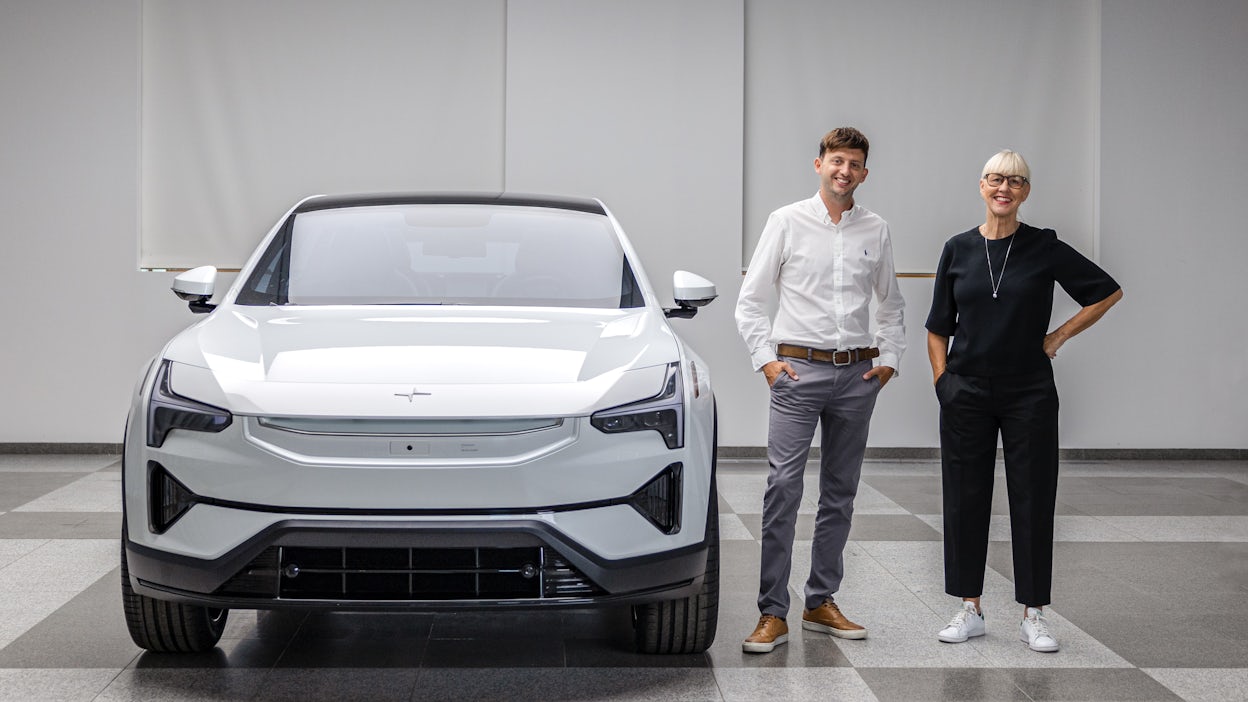
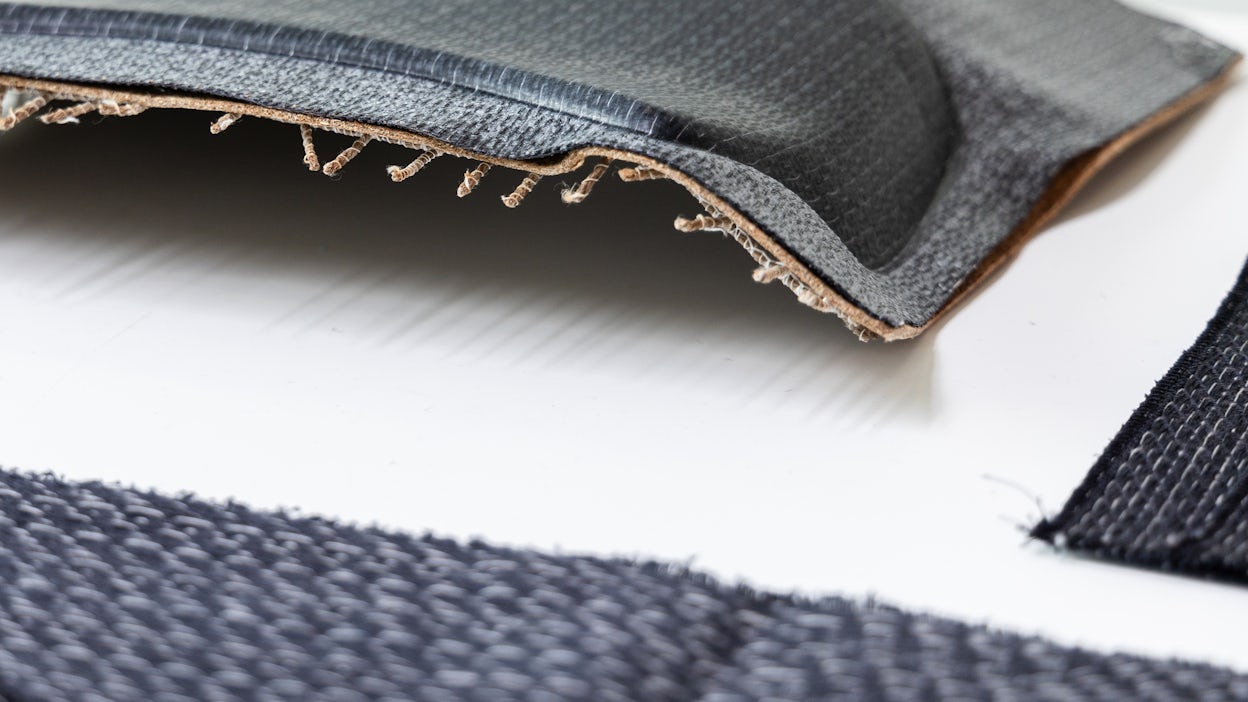
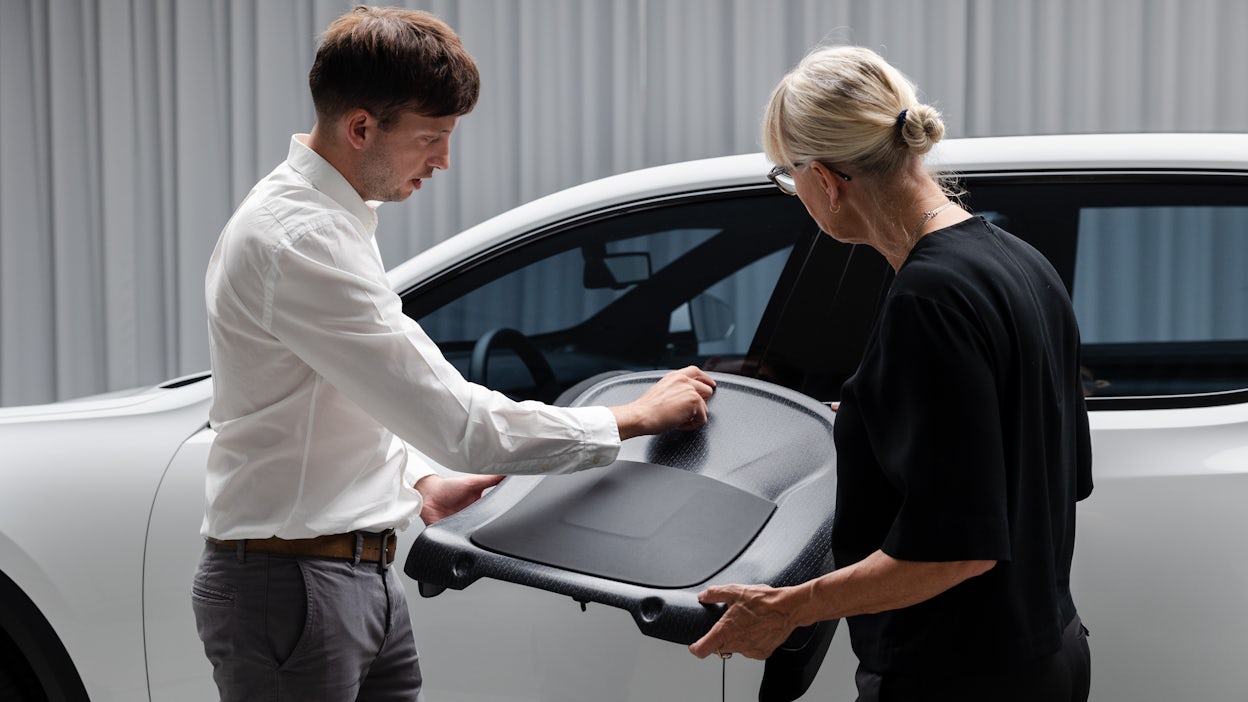
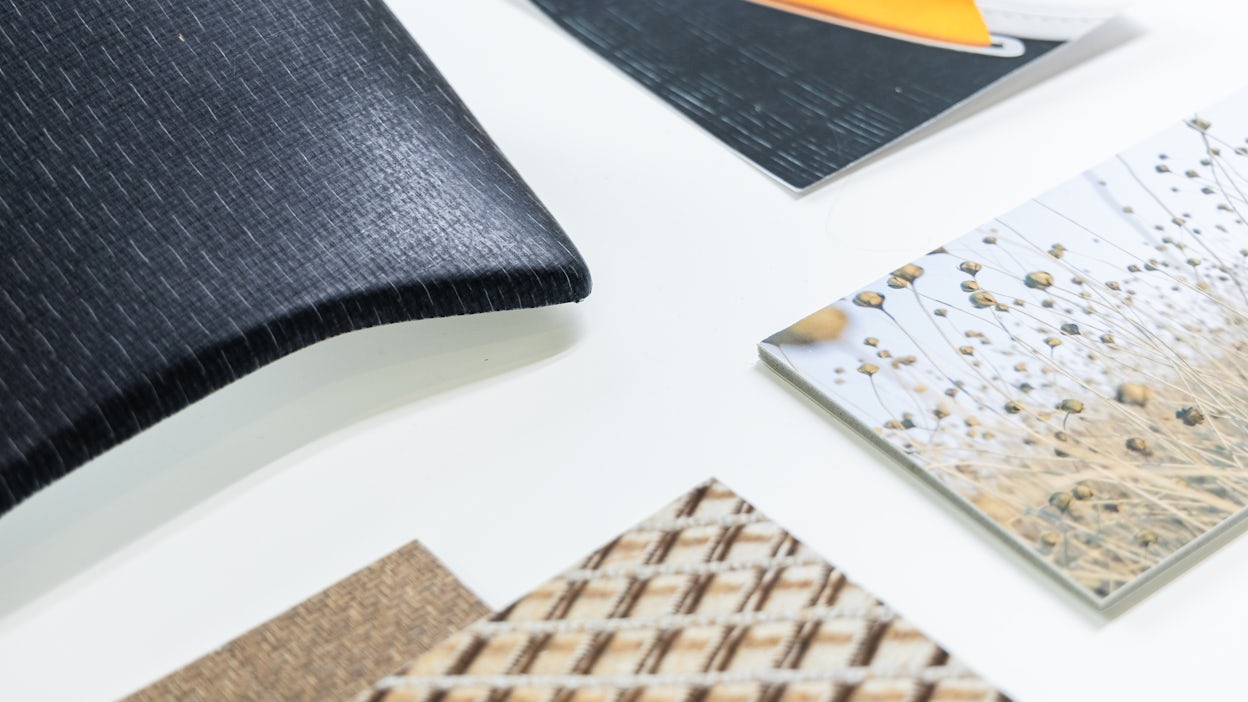
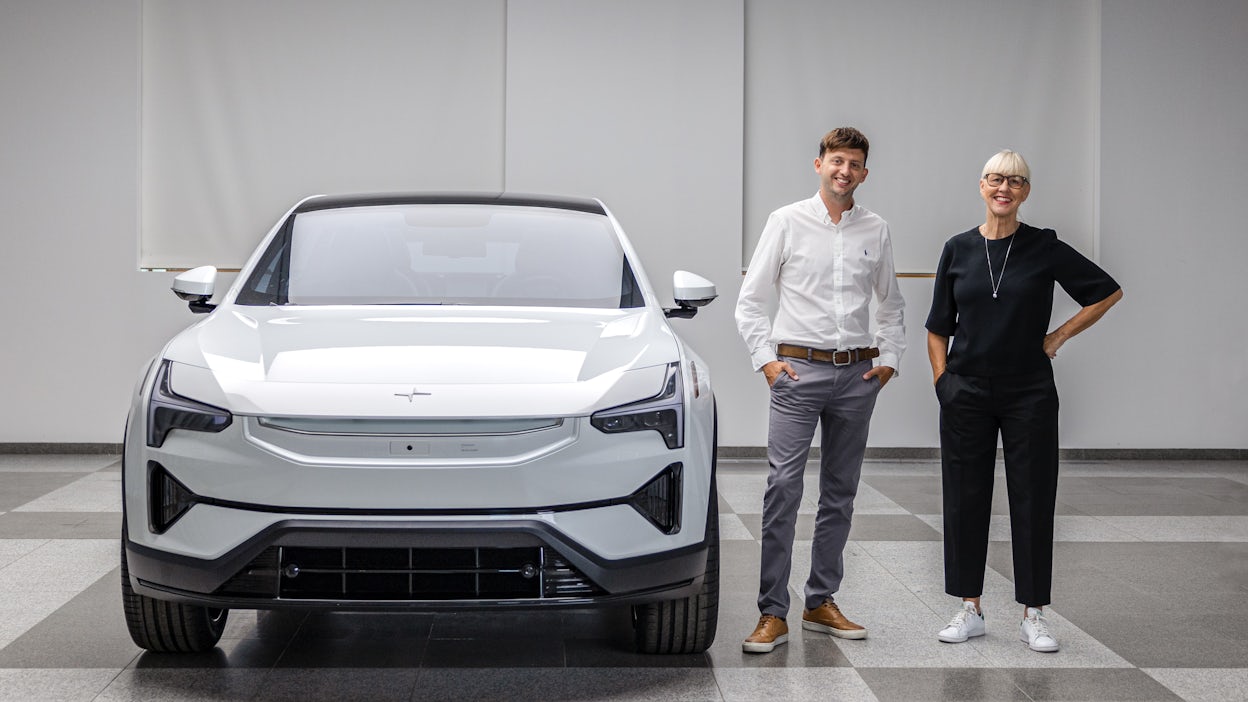
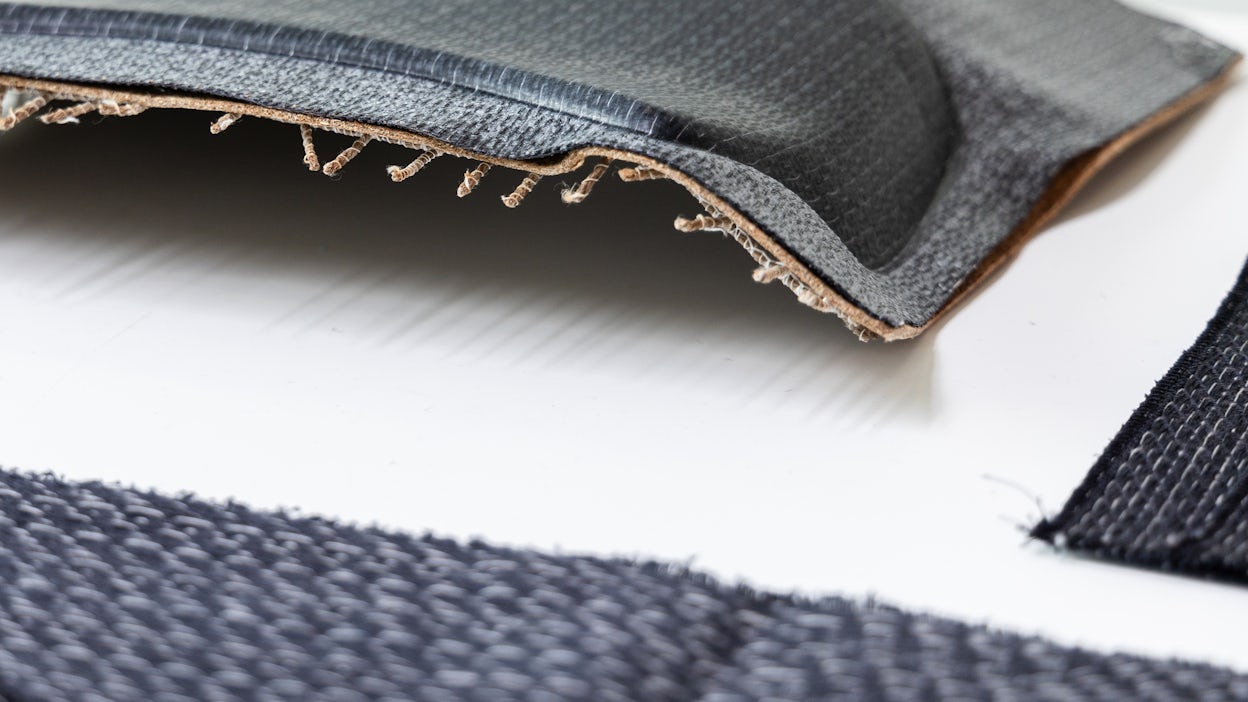
01/04
« Le pouvoir d’un designer est de créer un désir pour le bon choix, celui qui pointe dans la bonne direction », dit Maria Uggla, directrice des couleurs et des matériaux chez Polestar. « Toutes les matières ont le potentiel de se transformer en une expression luxueuse, et nous les aidons à se révéler. »
Cette approche a mené à des résultats, tandis que l’équipe de conception a réussi à produire une nouvelle esthétique qui rend palpable la fusion entre design, minimalisme et durabilité. « Il existe de multiples avenues dans l’exploration et la création de nouvelles expressions lorsque nous travaillons avec de nouveaux matériaux durables », poursuit Maria.
Le tissu emblématique de Polestar, une matière flexible, quoique robuste, est né à la suite d’une collaboration approfondie et a trouvé sa place dans les revêtements des sièges du Polestar 3. Mais ce parcours n’a pas été direct.
Un cheminement de trois ans a marqué l’effort intensif de développer Bcomp en une surface en tissu visible à l’intérieur de la voiture. Plusieurs défis se sont présentés : le matériau devait afficher une performance constante dans des conditions extrêmes, des chaleurs accablantes aux froids glacials.
Le design de tissu choisi est le résultat d’essais et d’expérimentations exhaustifs. Un mélange de fibre de lin flexible, d’un composé de fibres naturelles et de powerRibs™, diminue non seulement l’utilisation de plastique, mais contribue également à la réduction du poids.

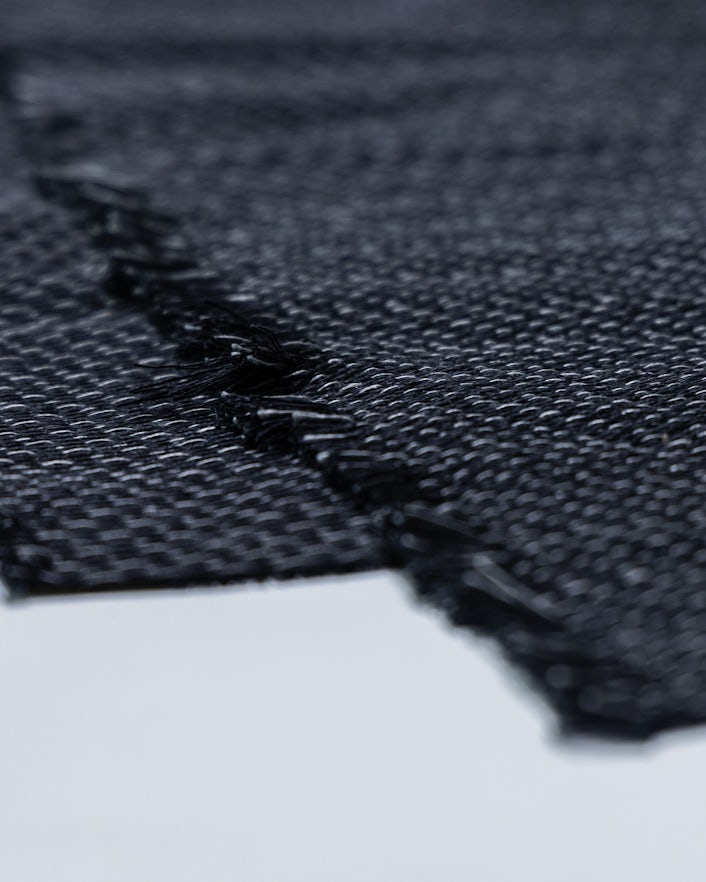
Le pouvoir d’un designer est de créer un désir pour le bon choix, celui qui pointe dans la bonne direction.
« Puisqu’il s’agissait d’une nouvelle façon de travailler pour nous, plusieurs défis se sont présentés tout au long du parcours. Voir le tissu est une chose, mais il en est une complètement différente de le voir transformé en un panneau. Il a fallu beaucoup d’essais, mais après avoir revu un bon nombre de versions, nous en avons choisi une en particulier, et elle est magnifique. J’ai très hâte de la voir dans la voiture », dit Maria.
L’optimisme quant à l’impact positif potentiel du projet sur l’industrie automobile était évident. Un bon résultat pourrait inspirer les autres équipementiers à adopter des matières durables similaires, fixant de nouveaux standards dans l’innovation durable.
« Pour nous, il est important que la matière soit de qualité. Il ne s’agit pas d’esthétique. Il s’agit d’une amélioration durable d’un panneau intérieur. Lorsque nous développons de nouvelles solutions durables, nous voulons nous assurer d’utiliser l’intégralité de leurs propriétés », dit Maria.
Le tissu emblématique de Polestar devait initialement faire ses débuts dans la Polestar 5. Cependant, le processus de développement accéléré et les résultats positifs des prototypes nous ont permis d’introduire la matière bien plus tôt que prévu. Mais notre parcours ne s’arrête pas ici. De nombreuses nouvelles applications sont déjà en cours d’essai, la performance et la durabilité seront optimisées, et de plus en plus d’efforts sont faits en faveur de l’économie circulaire.
« Habituellement, le travail créatif est réalisé lorsqu’une nouvelle technologie est introduite dans le processus de production. Dans notre collaboration, cela diffère : nous utilisons des données du processus de production pour développer de nouvelles approches et idées. D’une certaine façon, nous pensons en termes de générations », explique Ross.