Polestar Precept: From concept to car, episode 8
To progress, we must first assess. Attribute prototype cars are put through their paces to assess how well the different parts work, and how they can be improved upon.
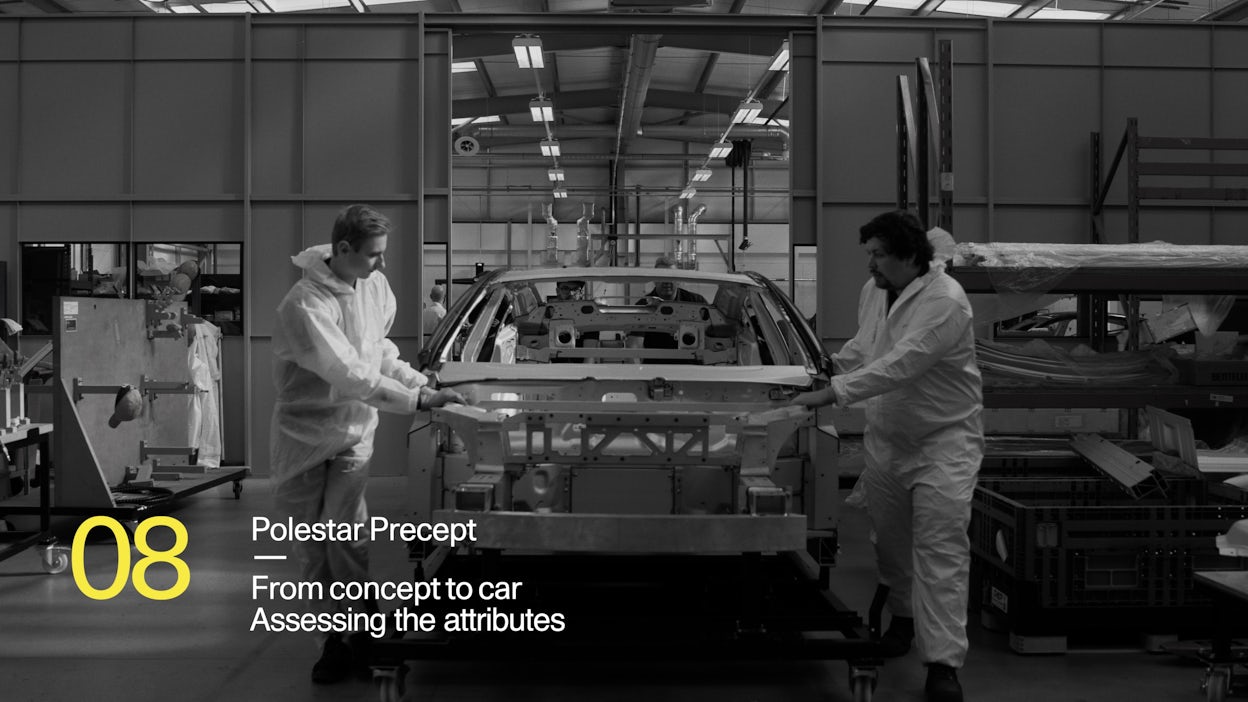
Turning a concept into a production vehicle requires real-world testing. For this, real-world cars are to put to the test. Hand-built for testing purposes only, attribute prototypes (AP) are created to assess how well different parts function separately and how they go together.In building AP cars, most of the assembly is done manually. From dry fitting the pieces to gluing the parts together, and oven curing. While in the manufacturing phase production cars will be assembled on automated production lines. Once assembled in the Polestar R&D facilities in Coventry, the AP cars are put to through various tests, such as high speed and low speed crashes, and structural durability tests. This is to help the R&D team assess certain attributes, learn of how the different parts go together, and progress towards creating a fully optimised production vehicle.Learn about the process of assembly, function, and testing of AP cars in episode 8 of the documentary series “From Concept to Car”.See all episodes and subscribe here.