«Dark Factories» und hochmoderne Robotik: So fertigen wir einen Polestar
Fabrikgebäude waren vermutlich nie die Art von Gebäude, mit denen man besonders angeben würde. Schmutzige, in die Jahre gekommene, düstere Objekte, die mit dem Kern einer Marke herzlich wenig zu tun haben. Doch Zeiten ändern sich. Automobilwerke der nächsten Generation sind intelligent, innovativ und grün. Da derzeit die ersten Polestar-4-Fahrzeuge aus unseren hochmodernen Produktionsstätten rollen (und auch die Produktion des Polestar 3 in den Startlöchern steht), öffnen wir die Türen zu einigen unserer Standorte rund um den Globus. Begleite uns und erfahre, was alles nötig ist, um ein leistungsstarkes und exklusives Elektrofahrzeug zu fertigen.
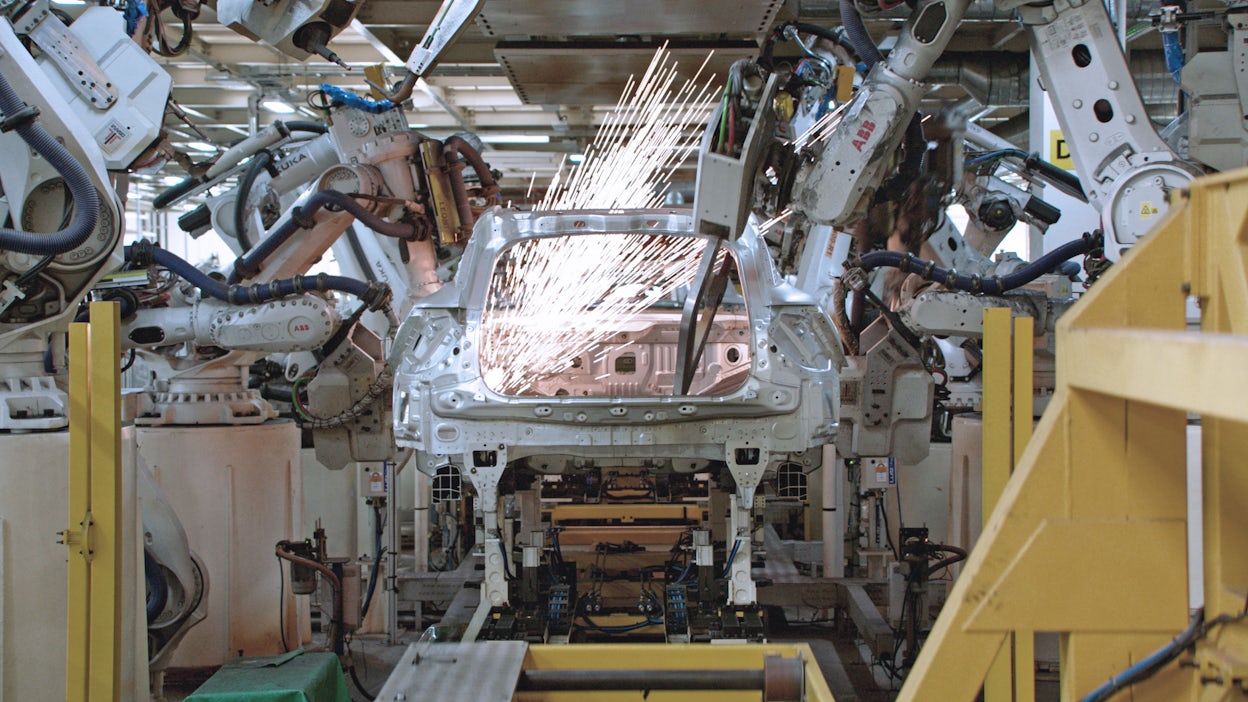
Die Herstellung von herkömmlichen Fahrzeugen ist ein komplexes Unterfangen. Nicht zu vergleichen jedoch mit der Herstellung von leistungsstarken Fahrzeugen der nächsten Generation – dazwischen liegen Welten. Mit Vehicle-to-Grid-Technologien, fortschrittlichen Fahrassistenzsystemen und einer Reihe anderer hochmoderner technologischer Lösungen unter der Motorhaube gehören unsere neuesten SUVs derzeit zu den modernsten Fahrzeugen auf dem Markt. Die technologische Komplexität gepaart mit einer einzigartigen Produktionsphilosophie schaffen eine ideale Grundlage für die Produktion eines Fahrzeugs.
Robotik und Big Data
«Was ihr hier seht, ist eine der modernsten Produktionsstätten weltweit», so Chunlin Zhao, Leiter des Polestar-Standorts Hangzhou Bay in China. Seit seiner Eröffnung im Jahr 2021 hat sich das Werk rasant als eines der innovativsten Automobilwerke der Region etabliert, das jährlich 300'000 Fahrzeuge produziert.
Der Standort, der aktuell für die Produktion des Polestar 4 verantwortlich ist, ist ganz vorne mit dabei, wenn es um zukunftsweisende Technologien geht. Mithilfe von Robotern, Big Data und Künstlicher Intelligenz wird sichergestellt, dass die Verarbeitung der Fahrzeuge auf höchstem Niveau erfolgt und die Effizienz des gesamten Fertigungsprozesses verbessert wird. Mit mehr als 3'000 Kontrollpunkten in der gesamten Produktionslinie werden in jeder Fertigungsphase umfassende Überprüfungen durchgeführt. Da Sicherheit bei uns sowohl in der Entwicklung als auch bei der Fertigung grossgeschrieben wird, überlassen wir nichts dem Zufall. «Wir sind dafür bekannt, dass unsere Fertigungsstätten über neueste technologische Entwicklungen verfügen. Wenn wir eine Lösung sehen, die unsere Prozesse verbessern kann, setzen wir alles daran, diese in unseren Standorten zu implementieren», erklärt Chunlin Zhao.
Das sind nicht nur leere Worte. Die Schweisserei in der Region auch als «dunkle Fabrik» bekannt, (da in ihr keine menschliche Fachkräfte arbeiten, die Licht für ihre Arbeit benötigen) verfügt über 800 vollautomatische, flexible Roboter, die in der Lage sind, hochkomplexe (jedoch stark repetitive) Präzisionsarbeit auszuführen. Im Datenraum wird ein unendlich grosser Informationsfluss in konkrete Handlungsanweisungen umgewandelt. Neigt sich der Bestand eines bestimmten Fertigungsteils dem Ende? Welche Roboter müssen gewartet werden? Alle diese Fragen werden in Echtzeit von einem Analysesystem bearbeitet.
Und dann ist da noch die Produktionslinie mit ihrer hochmodernen Megacasting-Anlage, in der grosse Fahrzeugteile in einem einzigen Stück aus geschmolzenem Aluminium hergestellt werden können. Die Anlage findet im Polestar-Produktportfolio derzeit zwar noch keinen Einsatz, zeigt jedoch die zukunftsweisende Richtung des Standorts. «Bei uns findest du Technologien, die du nirgendwo sonst auf der Welt findest», sagt Chunlin Zhao.
Doch während Roboter und Big Data den Standort auf ein ausgesprochen futuristisches Level heben, ist er aufgrund seiner Umweltverträglichkeit dennoch stark mit der Natur verwurzelt.
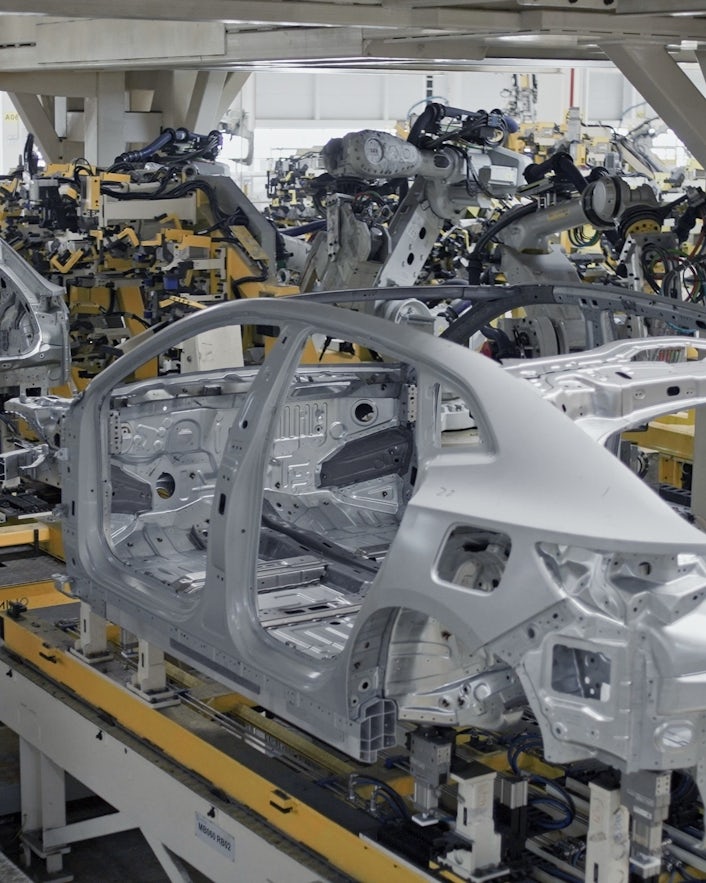
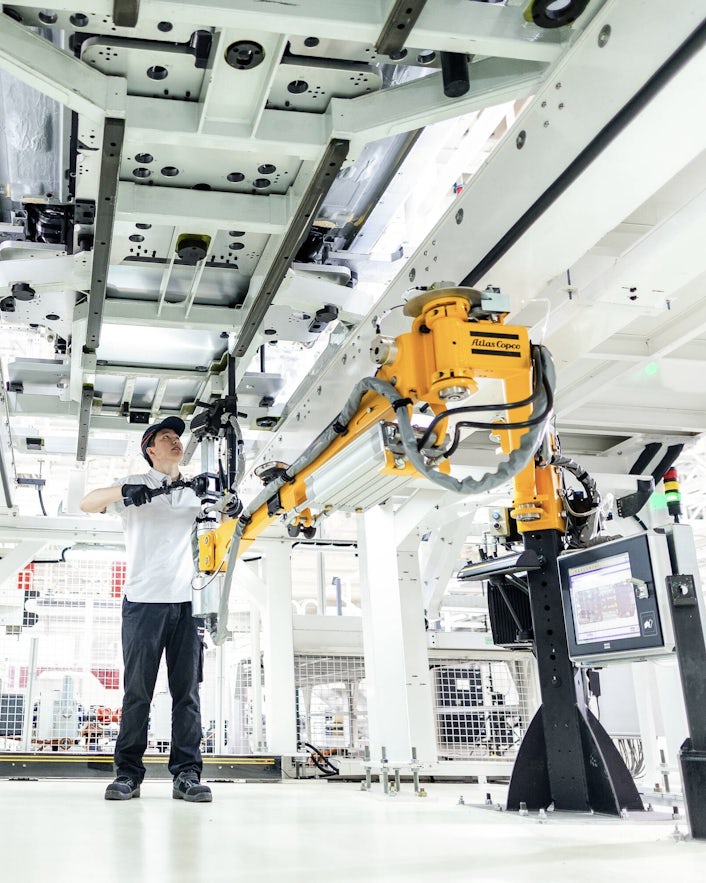
Wir sind sehr zuversichtlich, dass wir in all unseren Anlagen Kohlenstoffneutralität erreichen können. Das ist das Ziel.
Grüner Strom
In einer Branche, die derzeit versucht, dem Kohlenstoff den Rücken zu kehren, soll Hangzhou Bay den Status eines der saubersten Automobilwerke in der Region erlangen. Die Erwartungen an das Werk sind hoch, soll es doch den Polestar mit dem bei Markteinführung kleinsten ökologischen Fussabdruck produzieren. Mit Solarpanels auf den Dächern und Schmelzanlagen, die mit Wasserkraft betrieben werden, kommt der Standort den hohen Anforderungen jedoch ohne Weiteres nach. «Wir nehmen die Reduktion der Kohlenstoffemissionen in all unseren Fertigungswerken sehr ernst. Umweltaspekte werden bei jeder Entscheidung weitestgehend berücksichtigt. Angesichts unserer bisherigen Fortschritte sind wir sehr zuversichtlich, dass wir mittelfristig an all unseren Standorten Kohlenstoffneutralität erreichen können. Das ist das Ziel», so Chunlin Zhao.
Auf dieses Ziel wird entschlossen hingearbeitet. Nicht nur die Dächer der Anlage sind mit Photovoltaik ausgestattet, sondern sie verfügt über ein eigenes Solarkraftwerk, das jährlich über 48 Millionen kWh erzeugen kann. Zudem sorgt ein vor Ort installiertes Energiespeichersystem dafür, dass der Strombedarf für eine gesamte Produktionsschicht mit dem Solarstrom gedeckt werden kann.
Unser ökologischer Fussabdruck weltweit
Asien ist nicht die einzige Region, in der Polestar-Fahrzeuge produziert werden. Unser «Asset-light»-Ansatz, bei dem wir die bestehende Produktionsinfrastruktur von Partnerunternehmen nutzen, hat unseren Global Production Footprint stark verbessert. Dieser Ansatz ist in der Automobilbranche relativ neu, seine Flexibilität bringt jedoch unglaubliche Vorteile.
«Viele Leute sind sich nicht bewusst, wie kostspielig es ist, die Infrastruktur aufzubauen, die für den Bau eines Autos erforderlich ist. Für eine junge Marke wie Polestar ist die Verbindung zu Volvo und der Geely Holding sehr wertvoll. Die Möglichkeit, die Infrastruktur und Ressourcen zu nutzen, die normalerweise nur den grössten Playern der Branche zur Verfügung stehen, bringt verständlicherweise enorme Vorteile», erklärt Jonas Enström, Head of Operations bei Polestar.
Erfreulicherweise eröffnete das «Asset-light»-Konzept nicht nur den Zugang zu neuen Märkten, sondern auch zu neuen technologischen Fortschritten.
Über 12'000 Kilometer von Hangzhou Bay entfernt liegt das Volvo-Werk Ridgeville. Über 600 Millionen Dollar wurden in die Erweiterung der Anlage in Charleston (South Carolina) investiert, in der Volvos erstes Batteriemontagewerk in den USA entstehen soll. Und genau hier wird im Verlauf von 2024 – nach einer zusätzlichen Investition von 118 Millionen Dollar – auch die Produktion des Polestar 3 anlaufen.
Im gleichen Zug wird die Fertigung des Polestar 4 im Jahr 2025 im grössten Werk von Renault Korea Motors in Busan (Südkorea) starten. Das Beispiel dieses Joint Venture zwischen der Geely Holding und Renault zeigt die enormen Vorteile des Polestar «Asset-light»-Ansatzes ganz besonders gut auf. «Das Konzept bedeutet für uns, dass der Grossteil unserer Ressourcen in das Design und in die Entwicklung der weltweit besten Elektrofahrzeuge fliessen kann, da wir nicht in eigene Anlagen investieren, sondern von der Skalierbarkeit und der Expertise unserer weltweiten Partner profitieren können», so Jonas.
Das ist eine sehr beneidenswerte Position, in der wir uns befinden. Sie ermöglicht es, uns auf das zu konzentrieren, was wir am besten können. Nämlich die schönsten Elektrofahrzeuge der Welt zu entwickeln.